De la chanson de Robert Paquette; Moi j’viens du nordhttps://open.spotify.com/track/03LLLw6w4bKwqtRuvmjGfd?si=24fec84b3937498f
BIENVENUE! WELCOME !
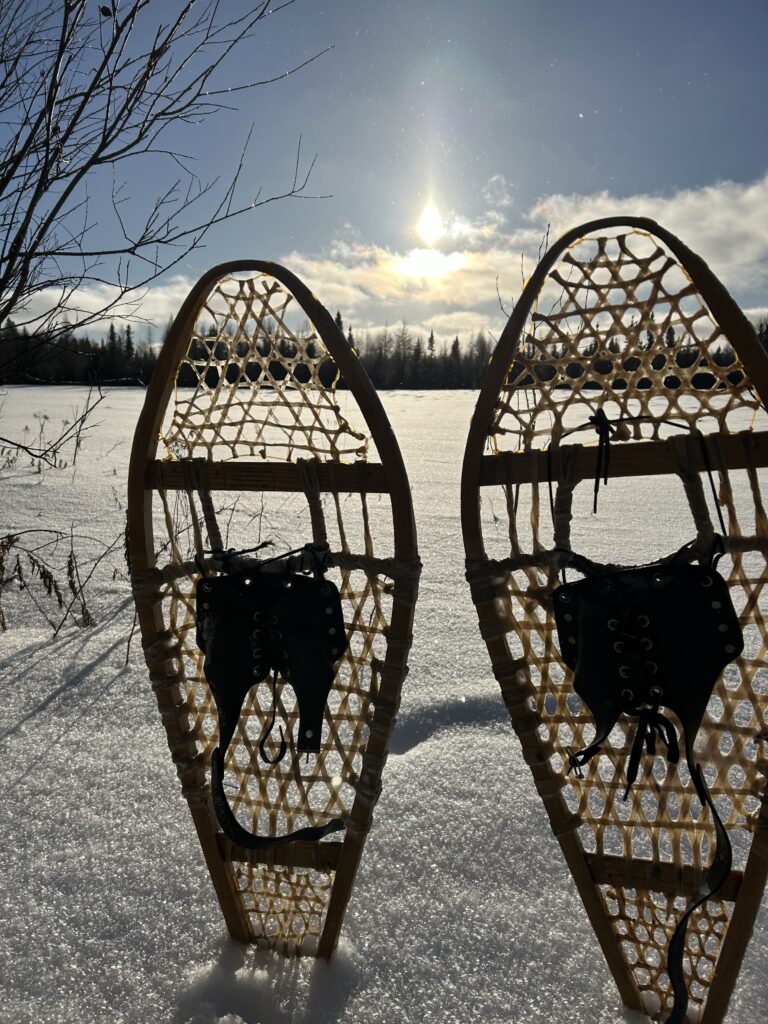
J’ai créé cette page d’abord afin démoraliser dans l’internet l’ncroyable histoire d’un homme qui s’est rendu à la Baie James apprendre des Crees comment fabriquer des raquettes. (faire défiler vers le bas).
Je suis depuis plusieurs années un fervent adepte de randonnées en raquettes, accompagné de mon chien Ali. Nous suivons les pistes que j’ai tracées dans la forêt. J’aime bien prendre des photos. C’est l’autre raison pour laquelle j’ai construit ce site afin de les publier ainsi que des textes au sujet de la raquette.
Si ça vous dit de m’envoyer des photos et ou des textes qui s’agencent avec le thème de ce site, ne vous gênez pas !
For several years now, I have enjoyed snowshoeing in the forest. I am accompanied by my dog, Ali. We follow trails I have cleared in the bush. I also like taking pictures. That is why I built this site in order to publish them as well as texts on snowshoeing.
If you would like to send photos and or texts that align with the theme of this site, please do!
Louis Corbeil
705-372-8694
CP; 2392
Hearst, Ontario. P0L1N0
LÉON LECOURS, TRAPPEUR/TRAPPER
The incredible story of a man who traveled to James Bay to learn from the Cree how to Build traditional snowshoes
Writen by; Louise Aubin, published by; Louis Corbeil
Blood, Mud and Beer
Léon Lecours has had a trap line since his boyhood. He is one of few professional trappers.
In retirement, he decided to learn to make traditional, hand-made snowshoes, as a hobby. In 2004, Leon travelled to Northern Quebec, near James Bay, to acquire the training for this dying craft, from First Nations Cree.
From 2004 to 2010, he completed 46 pairs of snowshoes for men, women and children. He was forced to stop practicing his beloved craft due to his health.
What follows is the process involved in fabricating each snowshoe. The entire process takes one complete year.
During the spring, the priority is to gather enough Black Ash and White Birch for an entire years’ requirement for his snowshoe orders. This wood is destined to form the Bases.
During the summer, the wood is cut and planed to the desired length and thickness; and soaked in hot water for one hour to make it pliable. The wood can then be set in a special jig to shape and curve it into Bases. The Bases are then dried (in the jigs to adopt its form) in the sun for 3 days.
Once thoroughly dried, the Bases are sanded and 3 cross pieces are affixed to hold the Bases together and provide support for the weaving and foot hole. In preparation for the Main Lines for the weaving, 1/8 inch holes are drilled 1 ¼ inch apart, along both sides of the Base, 10 ¼ inch long at the front and back.
During the fall it is hunting season and the best time to gather moose calf and deer hides since most hunters discard them. Calf hides are most desirable as they are thinner and therefore easier to cut and weave.
This stage of the process is long and arduous and appropriately named by Leon as the “Blood, Mud and Beer” time (certainly the trappers’ version of the expression “Blood, Sweat and Tears”).
Most of the work is done with the help of the Beam; two lateral, 6 inch in circumference PVC pipes (as used in plumbing) set at a 45 degree angle.
The other main tool is a double-edged straight Draw-Bar with one side sharpened into 45 de-gree cutting edge; and the other side is a 60 de-gree cutting edge. This tool was designed and fabricated by Leon and later provided to the Cree Natives who taught him the skill of snow-shoe-making.
The hides are hung on the Beam and with the Draw-Bar moving towards the cutter, the meat is removed from the inner hide. This is done outside or in the garage as it is quite messy.
The skins are then hung, one by one, on the Post; another hand-made apparatus to help secure the hide vertically to remove the hair by cutting it off with a knife, 1 inch at a time so the skin is not damaged.
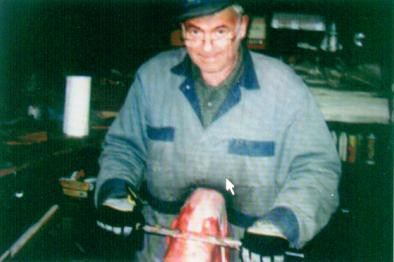
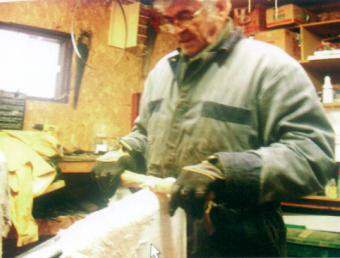
The First Nation Cree use a moose bone (cut be-tween the ankle and the knee; having removed the marrow and half opened in the middle; with sharp-ened edges), but Leon prefers the metal Draw-Bar.
During the long winter, the hides are again hung on the Beam to remove the under-fur. A temperature of minus 20 degrees Celsius is re-quired to thoroughly freeze the hides.
Generally, 12 moose skins and 70 deer skins are done at one time, requiring 20 minutes to freeze and 15 minutes each, to scrape the membrane off the skin. The frozen membranes fall in chips – again, a messy process which must be executed outside.
Let’s do the math on the time spent outside to complete this process: 70 + 12 = 82 hides @ 15 minutes of scraping in minus 20 weather = 1,230 minutes, or 20 and a half hours. This is when warm gloves and a buddy or two come in handy…
This entire process is enough to make 10 pairs of snowshoes!! Truly a labor of love for the art of snowshoe-making.
This process leaves a film of “under-fur”. The skins are kept moist and in a cold environment to keep them from rotting. You can understand Leon’s wife insistence on getting a separate re-frigerator!
One by one, the refrigerated hides are pinned to a 4’ x4’ plywood with small nails.
Two people are required for cutting Babiche: the cutter and another person to create the correct tension to facilitate the cutting process.
This hyde has undergone the entire process described so far. And now, Leon is ready for the intricate work of making “Babiche” and weaving it on the Bases.
Babiche is the name given by Natives, for the string-like material used to make the net-like filling in the snowshoe to keep the user walking on top of deep snow. The tighter the weave – the better.
Babiche is cut in a circular pattern, starting in middle of the hide, so there is a constant reposition-ing of the cutter. A special knife for this purpose was designed by Native Crees, enabling the Babiche to be cut in 1/8 inch thickness and 1/8 inch wide for deer skins; and 1/4 inch thickness for moose skins.
The freshly-cut Babiche falls into a bucket of water to keep it moist. One hide can yield up to 250 feet of Babiche (after countless hours of perfecting the cutting technique).
The long strips are then de-tangled and rolled into bundles as for wool, and either dried as do the Cree, since there is no refrigeration; or kept moist in the fridge until ready to use it. When dried, it must be again soaked before use so it is mineable for weaving; leaving both ends to dry so it will easily pass through the holes on the base. The deer Babiche is used for the front and back of the snowshoes, while the thicker moose calf Babiche is used for the middle of the snowshoe, so it will support the weight. Deer Babiche will shrink to 1/16 inch thickness when dry.
Now, the weaving of the Babiche begins. Women’s snowshoes require 320 feet of deer Babiche and 190 feet of moose calf Babiche; and takes 20 hours for the weaving. For Men’s: 340 feet of deer Babiche and 240 feet of moose calf Babiche; and takes 26 hrs to weave.
Leon recounts his challenge in learning how to weave without making errors. He started off by practicing with thick string and then with Babiche.
An elder Cree woman would just walk by, point at his would-be snowshoe, and say “mistake!”; leaving him to figure out where it was.
Hours upon hours were spent observing and learning from Cree women weaving effortlessly. He can now look at a photo of various weave patterns and spot the “mistake”. It is interesting to know that each tribe and region has their own intricate weaving design, making it possible to identify where and sometimes who made the snowshoes. A collector saw a photo of Leon’s snowshoes in a trapper’s magazine and was able to identify who taught him how to make them!
As an example, Leon provided me with a photo of a re-creation of the Penobscot snowshoes. Unlike the Cree and Attikamek which have matched geometric designs, the Penobscot shoes have 3 independent designs, all woven at the same time.
It took the collector 2 years to re-create the design. Only 4 pairs of this type remain – in museums. These, have not been crafted in the last 150 years of so. The collector in question challenged Leon to find any mistake in them and although he had to get the photo enlarged and used a magnifier, he man-aged to find 3 mistakes. Leon hopes to meet this col-lector some day.
The main Babiche lines are passed through the holes on the base, creating a triangular pattern.
The weaving is intricate and quite similar to knitting – where a mistake will show and would certainly be identified by a trained eye. I could not possibly attempt to describe the actual weaving… All I know is that it is a specific pattern, with lots of knotting in the appropriate places to secure the pattern and fin-ishing in the middle of each section.
Leon applies 3 coats of exterior varnish: Benjamin Moore #441 to preserve them and then installs the harnesses. Since the snowshoes were used on a daily basis, many reinforced the base of the Toe Hole as it is the most vulnerable spot, due to constant friction from each step. Some use Babiche, weaved over top so it can be readily replaced and others sewed a piece of hide for the same reason.
He prefers the rubber harnesses to the traditional leather as they are easier to slip onto boots and re-move. A man’s snowshoes can support a weight of 210 lbs and up, while lady’s snowshoes can support between 130 to 240 lbs.
Maintenance and Storage of Rawhide Snowshoes
Rawhide or Babiche must be varnished regularly to prevent hide from sagging. If it sags after usage, it must be slowly dried faraway from direct heat and generously varnished with an exterior oil-based var-nish.
Avoid letting wet hides freeze.
Store snowshoes in a cool dry place, sheltered from the sun and rodents.
Léon sold some of the snowshoes he built. The following is the ad he published;
ublished ; by Louis Corbeil